ダイキンのエアコンには、世界初の技術が数多く盛り込まれている。熱効率を高めるために、エアコンの要素部品の1つである熱交換器の性能を一層向上させようと、冷暖兼用マイクロチャネル熱交換機の新規開発に挑んだ、テクノロジー・イノベーションセンター(TIC) 主任技師・織谷氏に話を聞いた。
エアコンの省エネ性と軽量化・小型化のニーズに応えるために
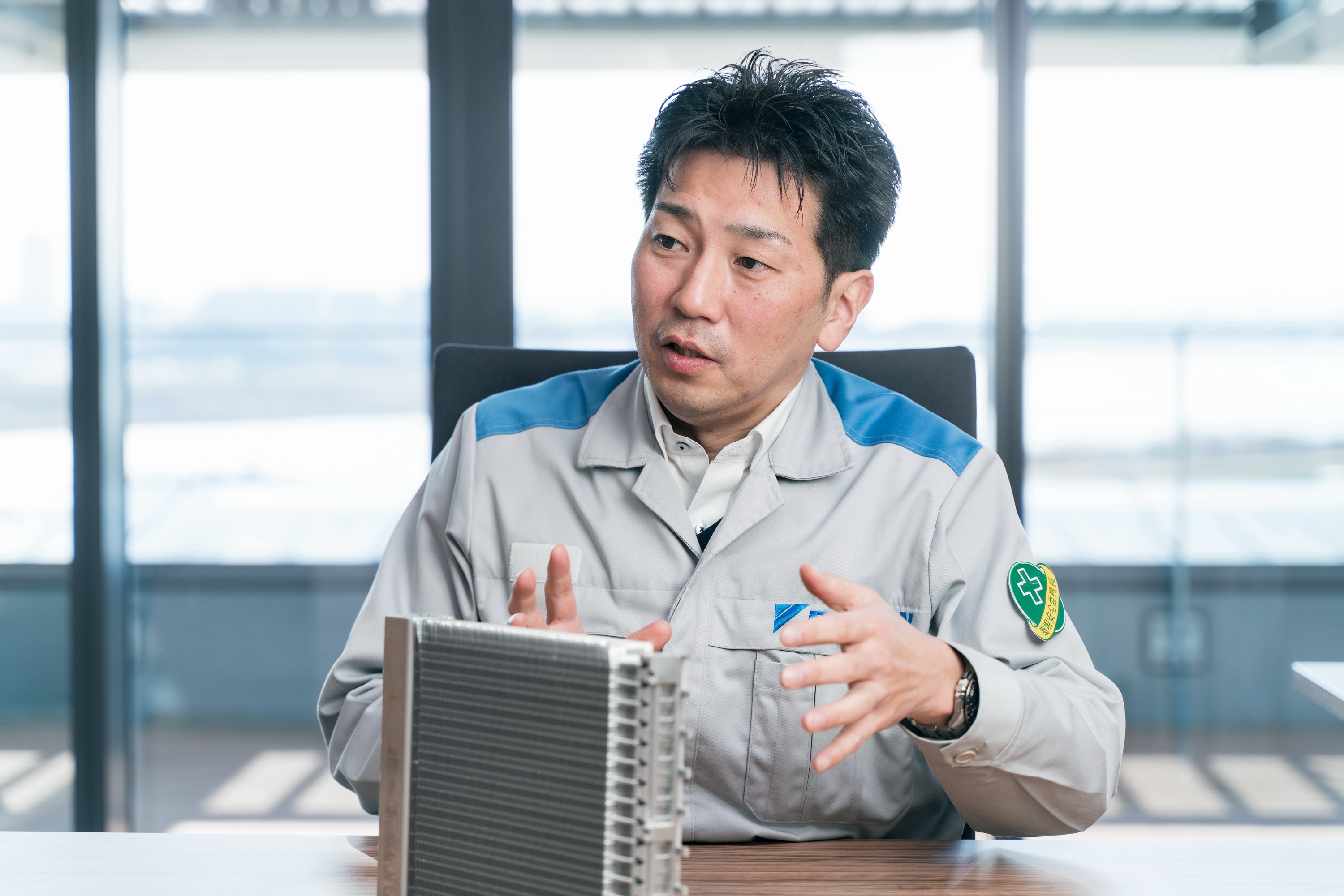
――入社するまでの経歴と入社後の担当を教えていただけますか?
織谷:ダイキンには2003年に入社したので、もう20年ほどお世話になっています。大学では熱流体の研究室にいたのですが、インターンシップ制度でダイキンで1カ月ほど働き、とても良い会社だと思ったので入社しました。2020年まで空調生産本部に所属し、熱交換器を中心に製品を開発してきました。それからTICに異動となり、ヒートポンプなどの先行開発、熱交換器、送風機の要素技術の責任者をしています。
――マイクロチャネル熱交換器の開発を進めることになった背景は?
織谷:このプロジェクトが本格的に動き出したのは2010年のことでした。地球温暖化防止の観点から、空調機器のエネルギー効率に対する規制が年々強化されてきていました。2015年に省エネ法の改正が決まっており、それに向けて業務用空調機の省エネ性能を向上させることが急務だったのです。空調機(室外機)には、心臓部の「圧縮機」と、背面にある「熱交換機」、風を送る「ファン」といった3つの主要素があります。そのなかで私が担当した熱交換器は、循環する冷媒から空気に熱を伝達させるものです。熱交換器の効率を上げるためには、一般的にはサイズを大きくする必要があります。
しかし、設置や搬入の観点からは軽量化・小型化が求められており、相反する問題を解決しなければなりませんでした。また環境負荷を減らすには、温暖化への影響がある冷媒を減らすことも重要です。そこで重量や冷媒量にとらわれず、高効率・小型・省冷媒を同時に実現する、まったく新しい技術に取り組むことになりました。
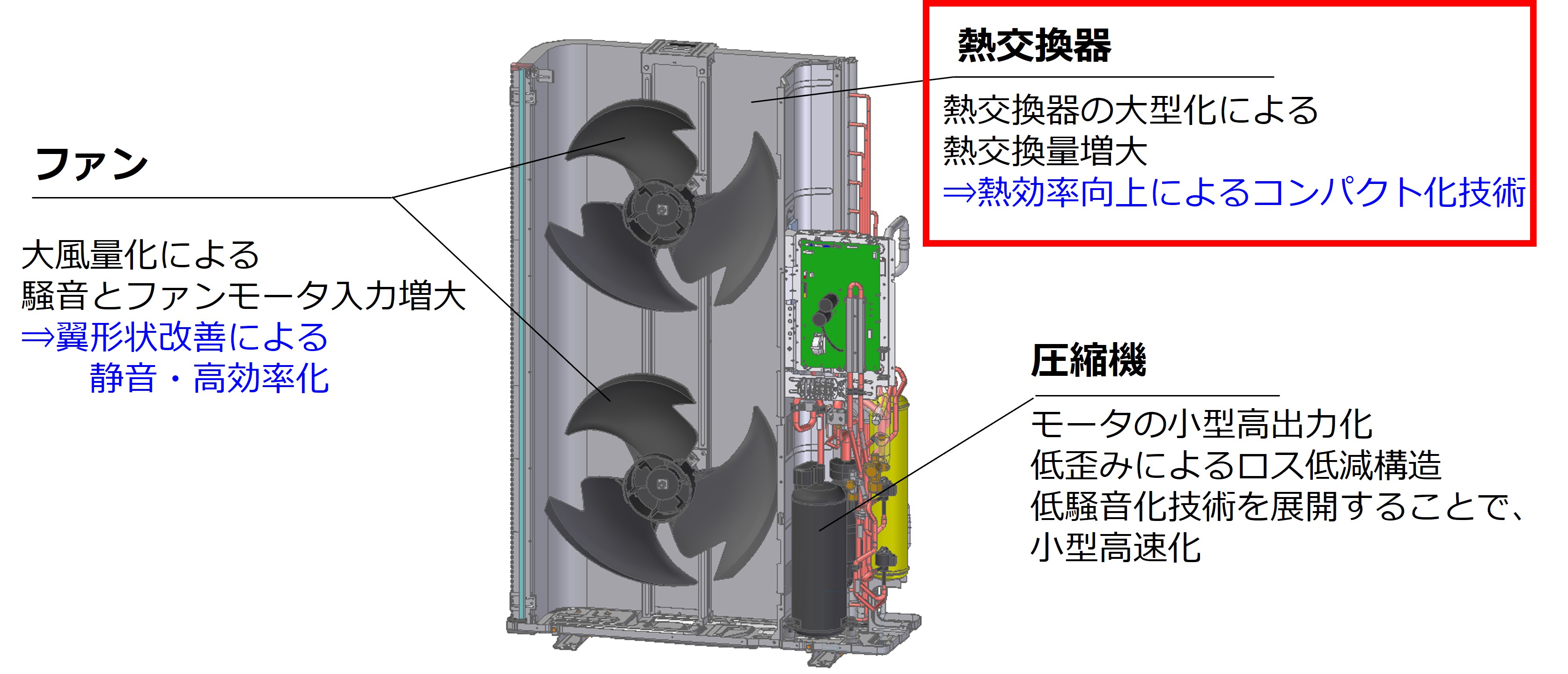
空調機のエネルギー効率化に向けた開発の方向性。エアコンの主要構成であるファン、熱交換器、圧縮機の課題を解決する必要がある
従来の技術だけでは限界 熱効率をいかに向上させるか?
織谷:一般的に熱交換器の熱効率を高めるためには、熱通過率を高めることが大切です。そのためには、アルミ板のフィンから空気への熱伝達率、冷媒が通る伝熱管の熱伝達率向上、さらにフィンと伝熱管接合部の熱抵抗低減という3つがポイントになります。
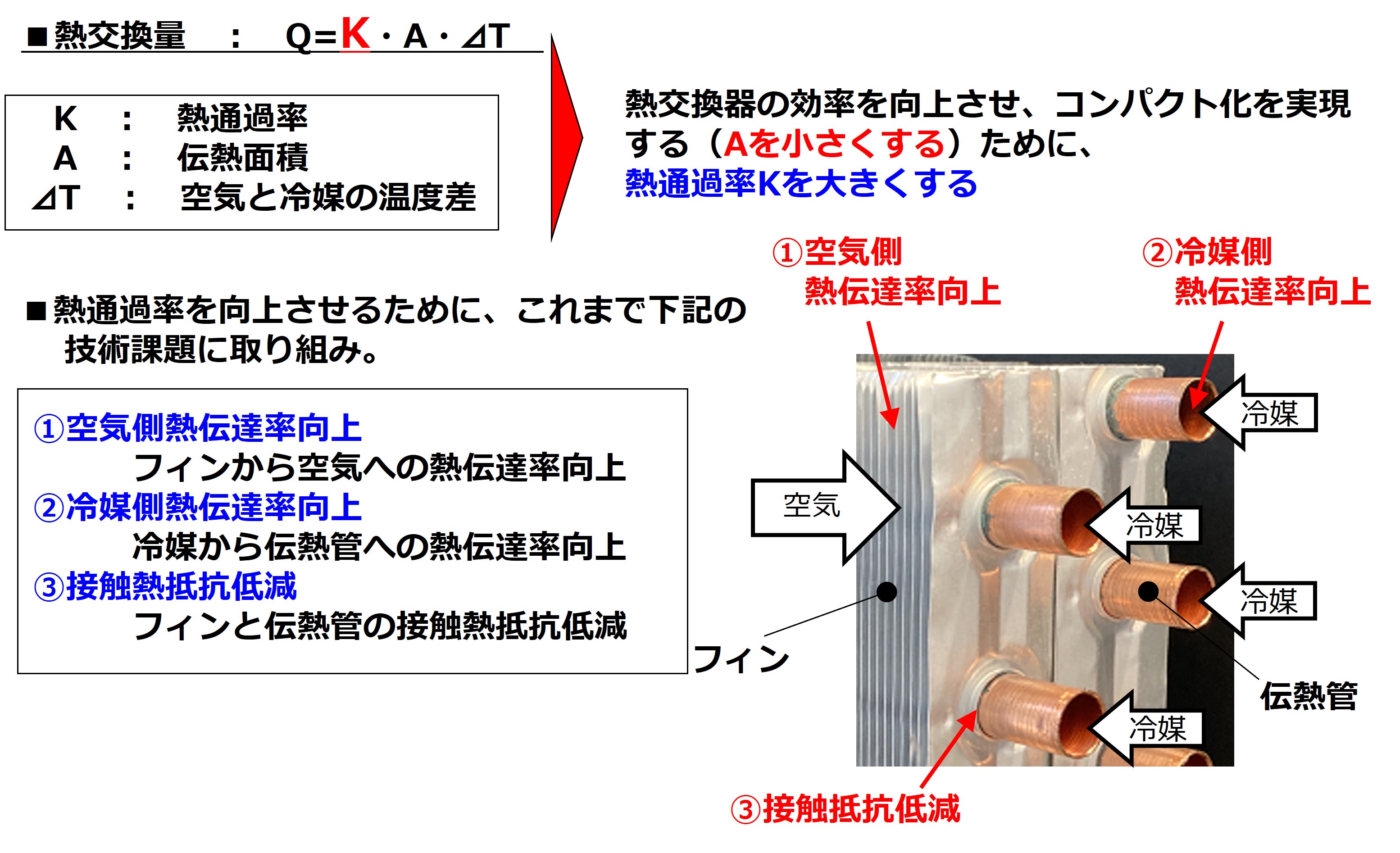
従来の熱交換機での効率化の取り組み。効率を向上させるための設計ポイントは、熱交換量が大きくなるように、熱通過率をアップすることだ。
まず空気側の熱伝達率ですが、伝熱管を細くすると、そこに当たる空気の通風抵抗が小さくなり、さらに伝熱管の配置を密にして高集積化できるため、熱が伝達しやすくなります。また、フィン形状を改良してスリットやルーパーなどを設けることでも、熱伝達性を高めてきました。
一方で、冷媒側の熱伝達についても、伝熱管に流れる冷媒の流速(流量)を増やしたり、伝熱管内面に溝を付けて冷媒を乱流にしたりすることで、伝熱効果を高めてきました。これ以外にも、機械的に接触させていた伝熱管とフィンの接合部をロウ付け(溶接の一種で金属で接合する)することで、接合部の隙間(空気層)をなくして熱抵抗を減らしています。
このように従来の熱交換器は60年以上にわたって改良されてきたのですが、ここ10年間で熱効率は10%程度しか改善できておらず、頭打ちになっているのが実情です。伝熱管の管径は最小4mmの加工限界に達しました。冷媒側の熱伝達は向上しましたが、伝熱管の圧力損失が大きくなり、パス数(管数)の大幅な増加が求められています。そこで我々が考えたのが、今回のマイクロチャネル熱交換器です。
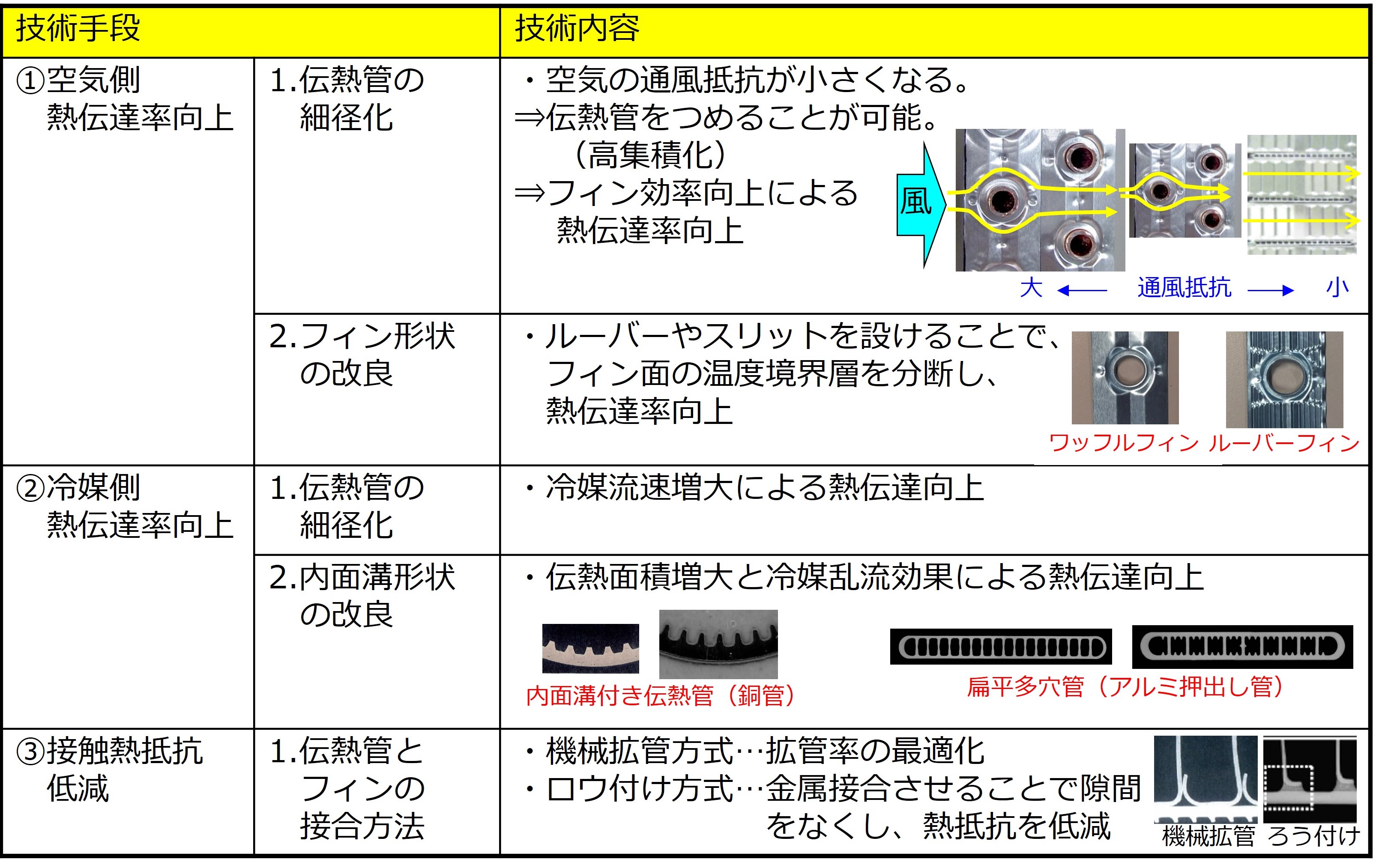
熱効率を高める3つの技術手段と設計のポイント。空気側と冷媒側の熱伝達率の向上、接触熱抵抗の低減を行うために、さまざまな工夫を凝らしてきた。
冷暖兼用マイクロチャネル熱交換器の開発における新たなハードル
――マイクロチャネル熱交換器とは具体的にどのようなものなのでしょうか?
織谷:マイクロチャネルとは、簡単にいうと冷媒用の細い流路のことです。実はマイクロチャネル熱交換器は自動車では一般的に使われていて、エアコンのガスを冷却する「コンデンサ」として搭載されています。また冷房専用機(凝縮器専用)の室外機にも搭載されていますが、これまで(暖房も兼ねる)業務用のエアコンには使われていませんでした。
従来のマイクロチャネル熱交換器の構造はこのようになっています。冷媒が通る伝熱管を円形から非常に細い扁平形状にします。この扁平管は穴の大きさが1mm程度という「究極の細径化」を施しています。さらに扁平穴同士の間に蛇腹(ジャバラ)状にしたアルミ製の「コルゲートフィン」を挟み込んで高積層化するのです。
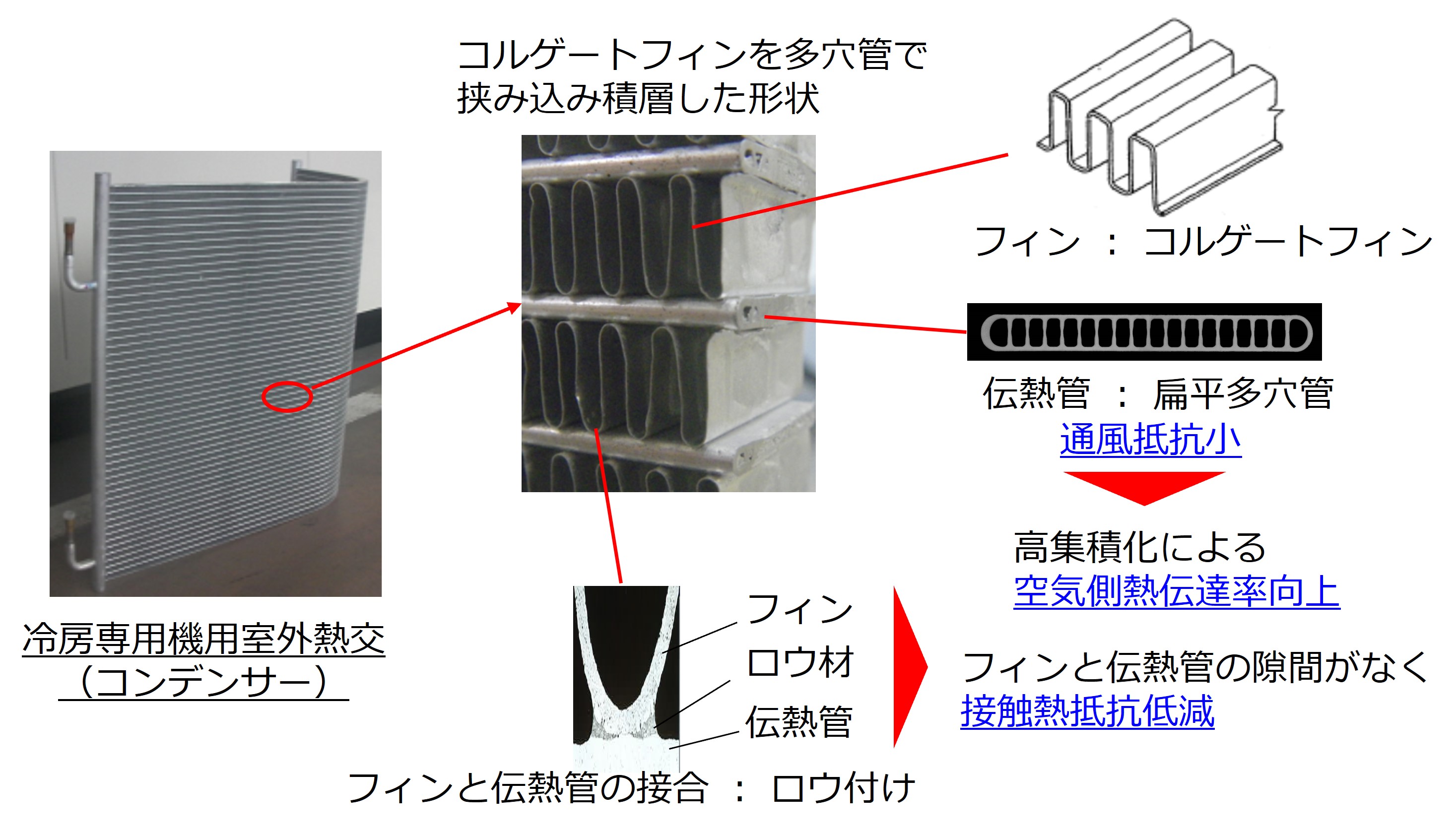
従来の熱交換器での効率化の取り組み。すでに冷房専用マイクロチャネル熱交換機はあったが、冷暖兼用のものは開発が難しかった。
――マイクロチャネルにすることで、どのような効果が得られるのでしょうか?
織谷:まず伝熱管を扁平形状にすると流路の抵抗が小さくでき、また何千もの冷媒流路を高集積化して配置できるので、フィンを通じて空気側に伝わる熱伝達率が向上します。材質はすべてを銅からアルミに変更したので、軽量化にも寄与します。フィンと伝熱管の接合はロウ付けしました。さらに管の高集積化により、全体の容積も減り(小型化)、冷媒量も減らせるのです。
ただし、マイクロチャネル熱交換器を冷房だけでなく、暖房としても使える冷暖兼用エアコンに採用するには、熱交換も冷媒を凝縮だけでなく、蒸発させる機能を具備しなければなりません。それには乗り越えるべき3つの課題がありました。
1つ目の課題はドレン水の水はけです。暖房で使用すると、室外機には空気中の水分が結露して「ドレン水」が発生します。ドレン水を排水しなければなりませんが、従来の構造ではフィンが上下に分断されており、ドレン水が流れ落ちていかないのです。そこで水はけ性を良くするために、ドレン水を落とす流路を新たに作る必要がありました。
2つ目の課題は、暖房時に冷媒が気体と液体が混ざった「2相状態」となることです。扁平管に冷媒を分流させるとき、2相状態である冷媒の、液体は重いため下側の管に集まり、気体は軽いので上側の扁平管に集まり、液体と気体が偏って分配されやすくなってしまいます。この偏りは熱効率の低下につながるため、冷媒の流れをCAEソフトウェアで解析し、冷媒を均等に分配する工夫が求められました。
また3つ目の課題は、発生したドレン水で管が腐食するというもので、アルミ材の耐食性を上げる必要がありました。
――では新開発のマイクロチャネルに対し、どんなアイデアを盛り込んだのですか?
織谷:1つ目の水はけ性の課題ですが、従来はフィンが上下に分断されていましたので、マイクロチャネルの扁平多穴管の横に流路を差し込んで、上下につながった新しいフィンと多穴管構造にすることで、排水性を向上しました。
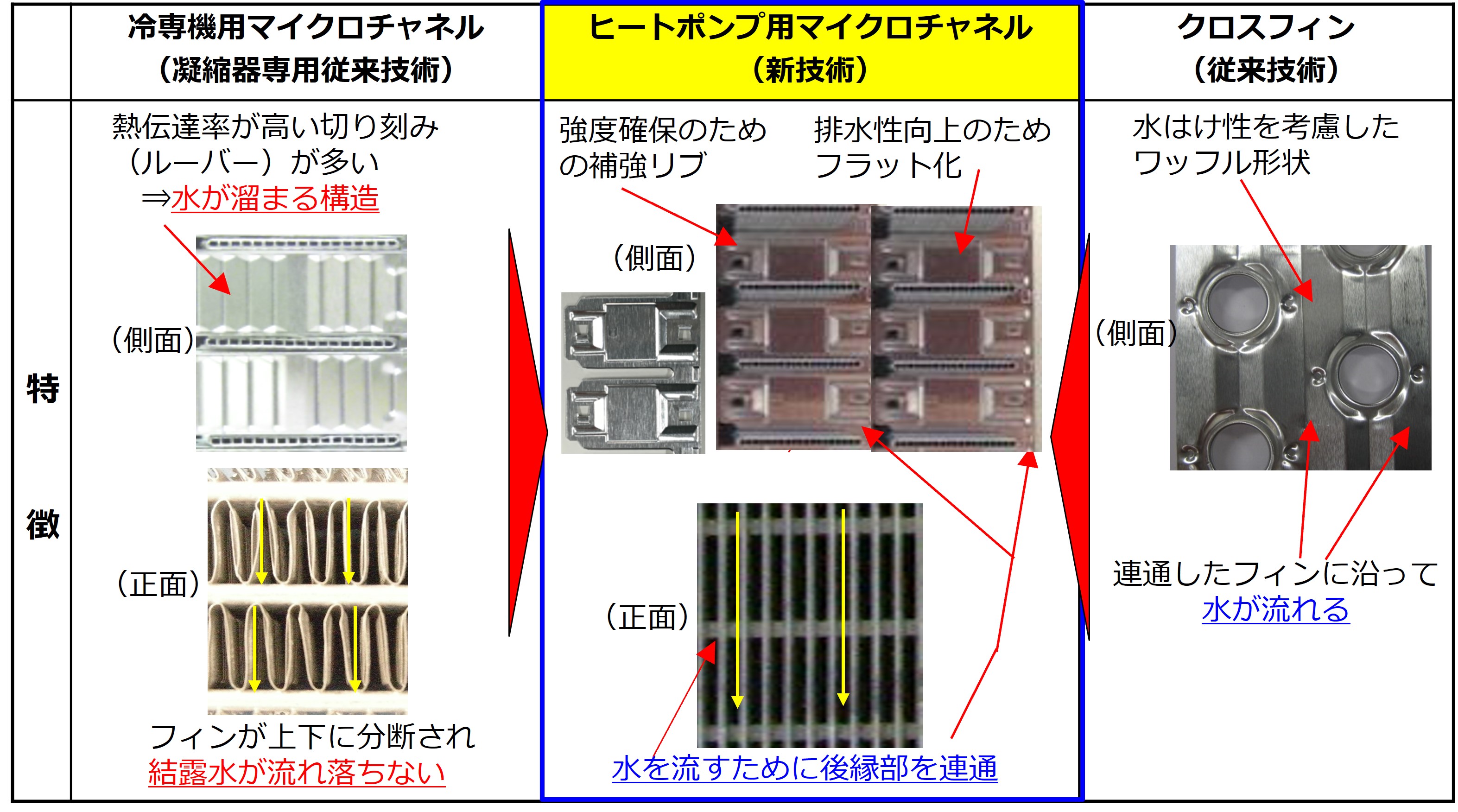
ヒートポンプ搭載機に向けた技術開発。扁平多穴管を横から差し込み上下に連通したフィンを設計し、ドレン水の排水性の向上。
2つ目の課題ですが、従来は冷媒を複数の管に分流させる場合は、単純に冷媒を下から上方に噴き上げていました。この方式だと冷媒の液体と気体の分配に偏りができてしまいます。そこで冷媒を下から上へ、上から下へと回す循環型にする新しいヘッダー(複数の扁平管を束ねた)分流構造にしたのです。これにより、ほぼ100%に近い分流性能を発揮できるようになりました。
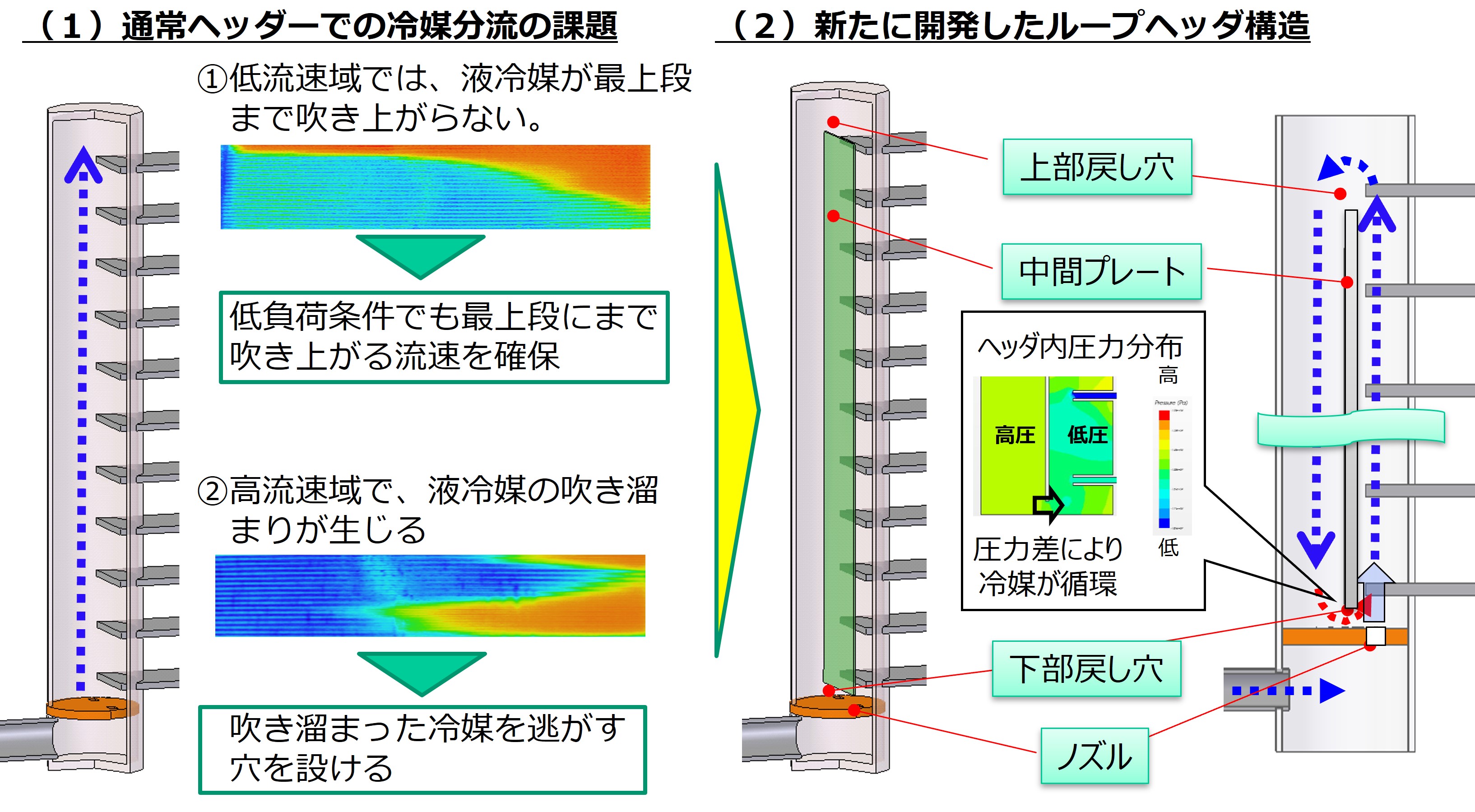
ヒートポンプ搭載機に向けた技術開発。暖房時に発生する冷媒偏流を抑制するために、新しいヘッダー分流構造を考案した。
3つ目の耐食性の課題に関しては、我々は材料技術を持っていなかったので、(株)UACJ(旧住友軽金属工業)と共同で開発しました。フィン、多穴管、ヘッダー、ロウ材はすべてアルミ製ですが、実際に亜鉛などの添加物の配合は微妙に異なっています。これによって、伝熱管の耐食性を向上させました。
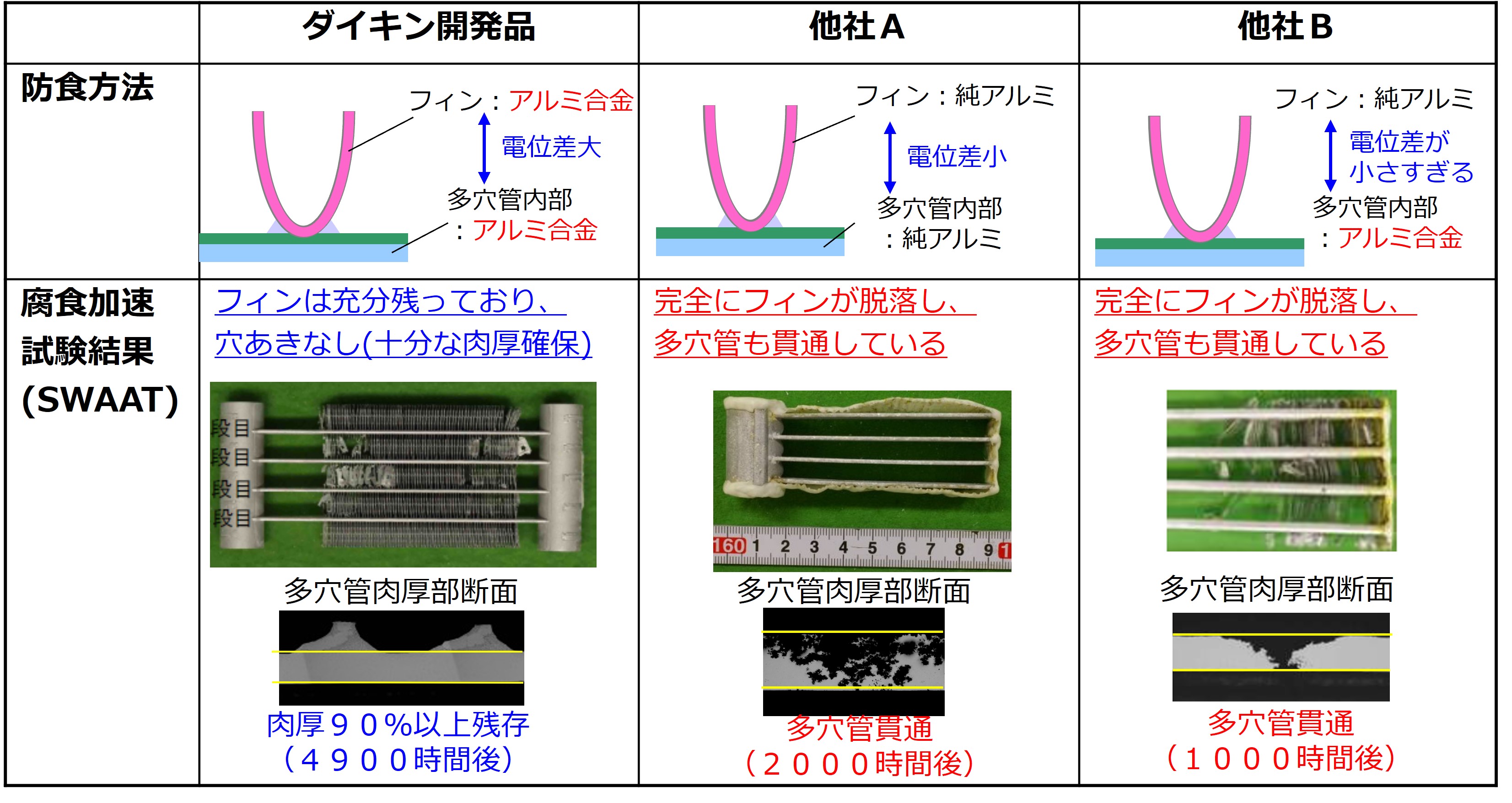
ヒートポンプ搭載機に向けた技術開発。純アルミでなく、亜鉛を微量に配合することで、耐腐食性を向上。
立ちはだかる量産化の壁。歩留まりが約100%を目指して関係者が一丸に
――今回のプロジェクトで、特に苦労され、それを乗り越えて感動した瞬間はありましたか?
織谷:詳細は省きますが、量産化する方法が全く新しい工法だったので大変苦労しました。フィンに扁平多穴管を挿入する工程では、フィンが「ぐにゃり」と座屈してつぶれてしまうのです。どのくらいの寸法公差に収めればよいのか分からず、半分ぐらい不良が出てしまいました。開発者も生産ラインに張り付き、どの工程でどんな不良が起きるのか、データを取って徹底的に調べました。ようやく1年かけて、良品率はほぼ100%になりました。そのときはみんなで大喜びしましたね(笑)。
あとはフィンと多穴管のロウ付け工程も難しかったですね。これまでは部分的に接合していたのですが、新しい製造工程では熱交換器全体を巨大な窯(炉)に入れ、電子レンジのように熱しながら、フィンと多穴管をアルミでロウ付け接合しました。我々にとってはこれも初めての経験だったので、最初はロウ付けの不良がけっこう出ました。そもそも自社の製造ラインには窯もなく、プロトタイプを作ることも難しかったのです。そこで(株)UACJの名古屋工場に半年間ほど通い、ロウ付けのノウハウを学び、窯についても検討させていただきました。
――量産化のハードルを乗り越えるために見えない陰の努力の積み重ねがあって、完成化にこぎ着けたのですね。
織谷:そうですね。なんとか冷暖房兼用ヒートポンプ室外機に、世界初となるオールアルミ製のマイクロチャネル熱交換器を搭載することができました。2012年に発売した業界最小の「スカイエア ZEAS(ジアス)シリーズ」に初めて投入され、機器の重量も80㎏から59㎏まで軽量化し、小型化にも成功しました。それに伴って省冷媒化もでき、CO2排出量も減りました。
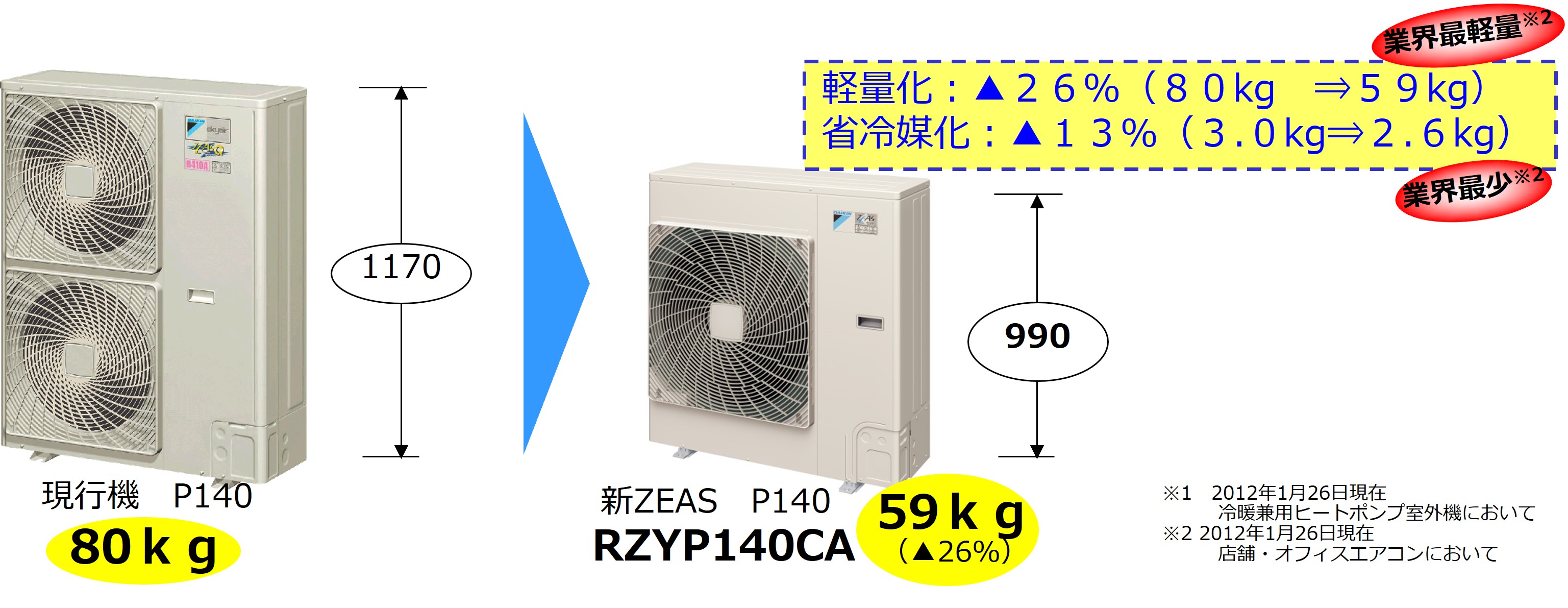
2012年に発売された「スカイエア ZEASシリーズ」。開発したマイクロチャネル熱交換器を搭載し、環境性・軽量化・コンパクト化を実現。
さらに2015年には、ZEASシリーズをブラッシュアップした新機種を発売しました。こちらは2機種あり、最上位機種で省エネ性能No.1の「FIVE STAR ZEAS」と、小型化した「Eco-ZEAS」を用意しました。また2018年に発売したビル用の大容量室外機「VRV6シリーズ」にも、このマイクロチャネル熱交換器が採用されました。
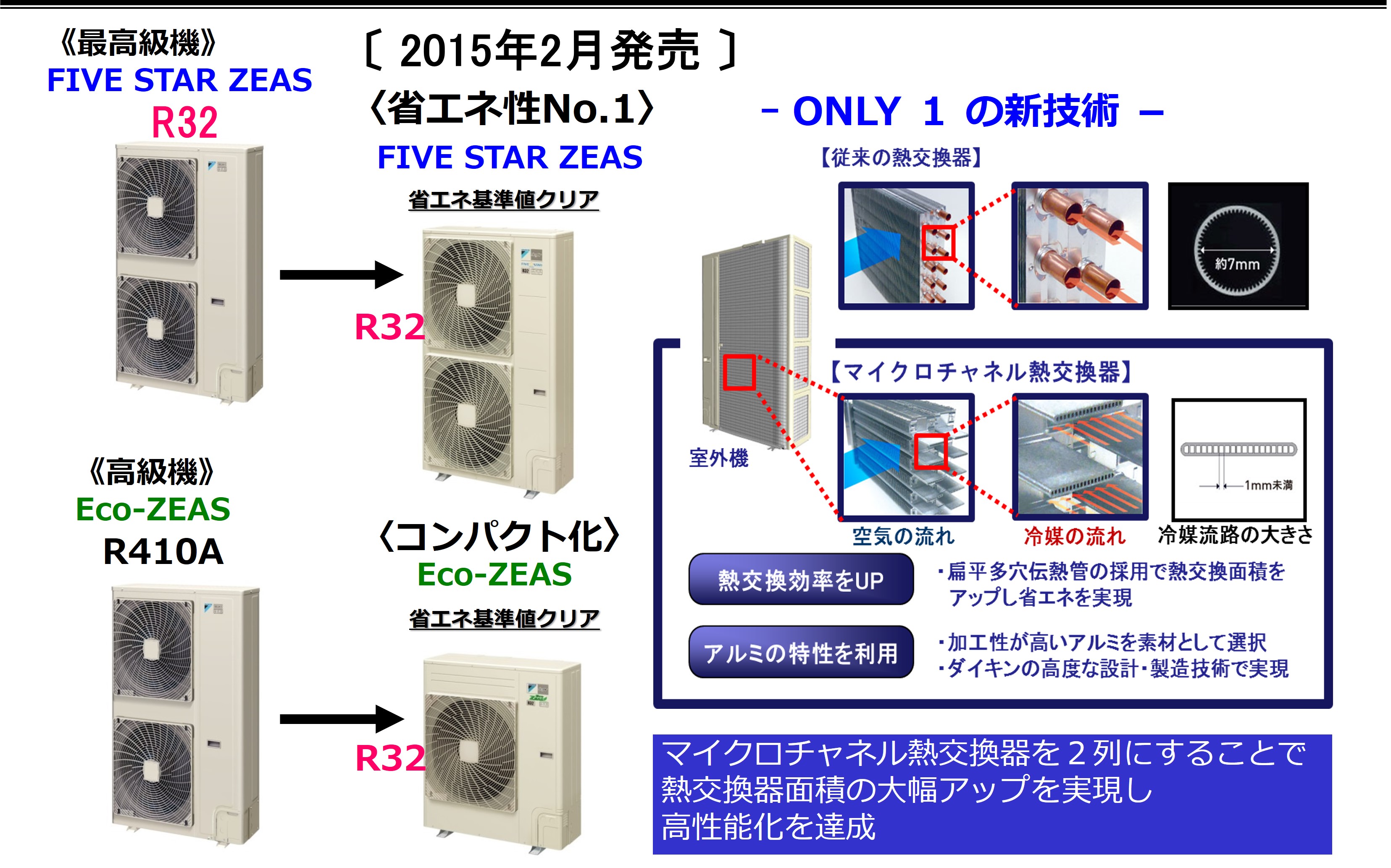
マイクロチャネル熱交換器を搭載し、さらにブラッシュアップした2機種も2015年に発売。これらは省エネ性No.1と、コンパクト化を実現している。
――最後に、これからダイキンに入社を希望する将来の後輩に向けて、何かメッセージをお願いします。
織谷:冷暖兼用のマイクロチャネル熱交換器のように、これまでにない新しい開発をするには、コストも時間も掛かります。こういった開発は、エアコン専業メーカーの我々だからこそできるものだと思っています。ダイキンの良いところは、やると決めたら、関係者が一丸となってすごい勢いで集中して物事に当たることでしょう。実際にそれを後押しする環境や風土があります。ぜひ新しいことにチャレンジしたい方は、我々の仲間に加わって下さい。
Yoshio Oritani
テクノロジー・イノベーションセンター 主任技師
2003年4月入社。大阪府出身。冷凍サイクル技術、熱交換器技術、送風機技術担当。
やるからには世界でNO.1の技術者集団にし、世界に名前を残すような技術開発に挑戦し続けたい。
関連記事
関連採用情報