インバータは、エアコンの圧縮機などに使われるモータを自在にコントロールするために不可欠です。オン/オフの単純な制御ではなく、インバータ技術を使えば、回転数を滑らかに微調整して、ムダなエネルギーを減らし、省エネ化に貢献できます。このインバータ制御回路に不可欠だった電解コンデンサを大胆にも不要にする技術を業務用のビル用マルチエアコンで実現したのが、土居さん。当時の開発の苦労について伺いました。
大学時代でもダイキンでもインバータ! インバータと共に歩む
――入社前、どんな学生時代を過ごしましたか? ダイキン工業を就職先に選んだ理由はなんでしょうか。
土居:子供の頃から、機械をいじったり、分解したりするのが大好きでした。高校は理系コース、大学も電気工学科に入りました。将来は電気関係の仕事に就きたいと思っていて、卒論もインバータの最適制御を選びました。ダイキン工業に入った理由は、生まれも育ちも関西だったので、関西圏から離れたくなかったことが大きかったのですが、ダイキン工業のコア技術であるインバータが、大学で学んでいたことと同じで学生時代に学んだ知識を活かすことができ、かつ世の中の省エネに貢献できると思い、迷わずに入社しました。
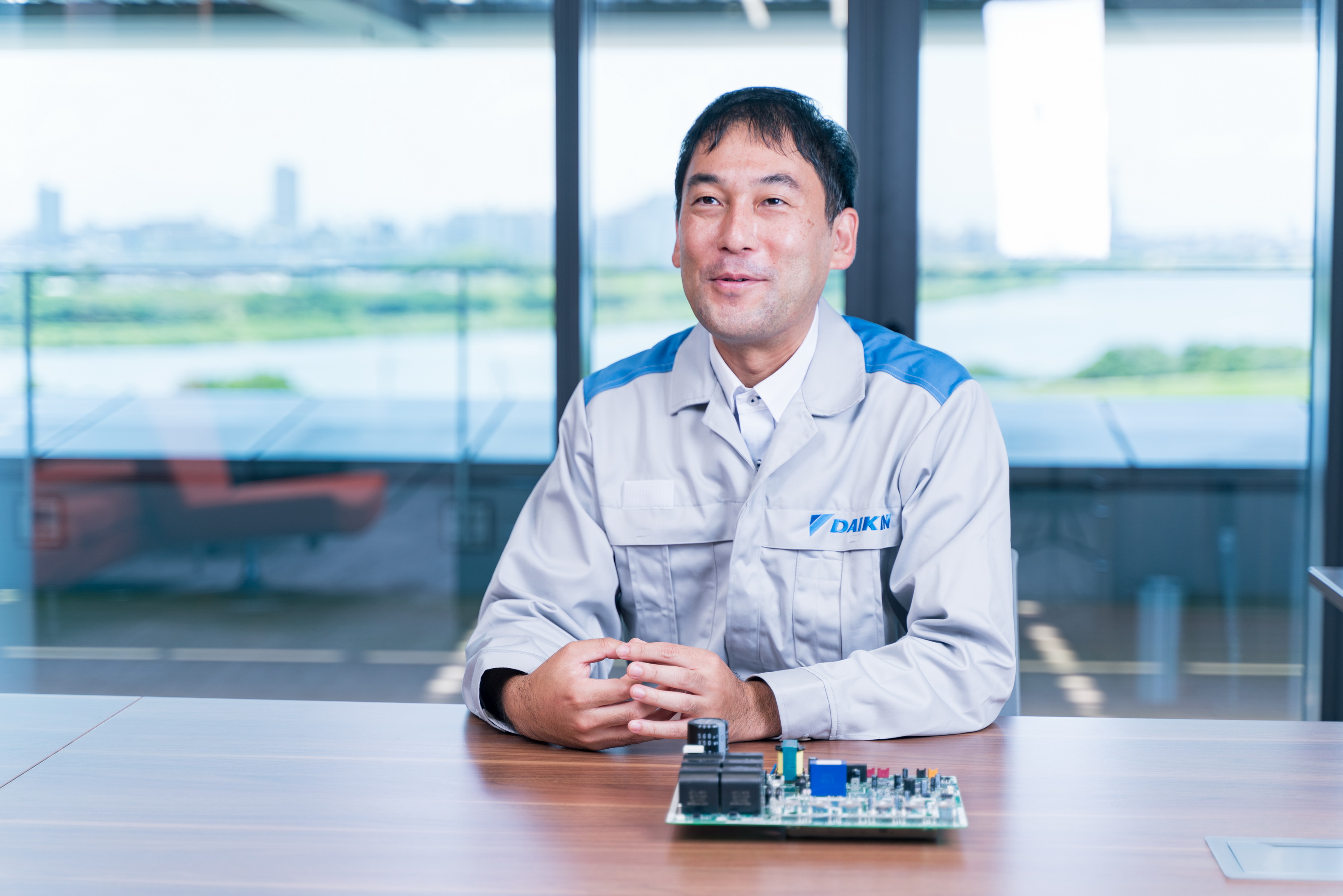
――入社後は、どのようなキャリアを歩んできたのでしょうか?
土居:2005年に入社して、今年で17年目です。入社後、業務用エアコンの部署に配属されて、2013年まで8年間、新製品の開発にどっぷり浸ってきました。そこでもエアコンのインバータの開発が中心でした。
ダイキン工業に入社してインバータに関わる仕事がしたいと思っていたので、入社以来、希望通りの部署に配属してもらい、恵まれた環境で過ごしてきました。ずっとインバータと共に歩んでいる人生ですね(笑)。
――三相電解コンデンサレスインバータの開発は、いつ着手し、メンバーは何人ぐらいでしょうか?
土居:業務用のビル用マルチエアコン向けのインバータを電解コンデンレスにする企画が最初に持ち上がったのは2013年頃のことです。開発期間は4年(技術開発に3年、量産開発に1年)ぐらいでした。技術開発でのメンバーはハード設計が私を含めて2人、制御担当が3~4人、モータと圧縮機の担当が各2人で、総勢10人ほどでした。
最初の2年間で新しいインバータのプロト機を完成させました。スピーディに開発できたのは、やはりゼロからの開発ではなく、すでに実現していた家庭用エアコンや店舗エアコン向けの電解コンデンサレス技術があったからです。ダイキン工業の技術資産をしっかり引き継ぎ、最速で立ち上げることができました。3年目には、モータや圧縮機に接続して整合性を調べ、各所に性能をアピールしながら製品搭載できるように走り回りました。ラストの1年は量産化に向けた最終調整を行いました。
常識に捉われないダイキンの発想が、電解コンデンサを不要にした!
――インバータの制御回路から電解コンデンサを取ってしまうという大胆な発想は、どうやって生まれたのでしょうか?
土居:そもそもインバータにおける電解コンデンサの役割は、交流電源から整流器を通して直流に変換された電圧の変動を和らげ平滑化し、一定の安定した電圧をインバータへ供給することです。電源が不安定では、インバータの制御にも影響が出て、モータのトルクが変動したり、回転時にうなり音が発生したりして動作が不安定になります。そこで、安定化のための電解コンデンサを配置することが、当時の常識だったのです。
しかし、電解コンデンサは寿命部品で経年劣化があり、寿命も比較的短いので、インバータ自体の寿命を決定する大きな要因になります。そこで寿命レスのインバータを目指すには、電解コンデンサを取りたかったわけです。ダイキン工業は当たり前に捉われない会社なので「インバータにはコンデンサが不可欠」という固定観念から抜け出せました。家庭用インバータでは、すでに10年前から電解コンデンサレスを実現していました。ただし、家庭用は単相電源で容量も小さいのに対して、業務用は三相電源で容量も大きかったため、さらに新たな技術開発が求められていたのです。
家庭用エアコンに使われている単相電解コンデンサレスインバータの回路構成。今回は業務用エアコンなので、電源は三相となる。
たとえば、業務用では当時、基板上に大容量の電解コンデンサを6個も搭載していました。それらを取り去って約30分の1の小容量コンデンサに変更し、コストダウンを図りました。この技術によって、従来インバータに比べて約40%のコストダウンが実現できました。というのも電解コンデンサの削除だけでなく、力率(流れる電力のうち有効活用される割合)を改善するリアクトルの小型化や、電解コンデンサを充電するための充電回路の削除も可能であり、電解コンデンサレス化はコストダウンと同時にインバータの寿命も伸ばせるため、一挙両得の技術なのです。
電解コンデンサありの従来基板と、電解コンデンサレスに改良した新基板の比較。960μF×6個=約6000μFの電解コンデンサが、30μF×6個=180μとなり、容量を30分の1削減し、コストダウンできた。
他者の追従を許さないダイキン工業の「インバータ波形制御技術」がベースに
――ダイキン工業がコンデンサレスを実現できた理由について教えてください。
土居:電解コンデンサをレス化すると電圧の平滑化する機能がなくなるため、インバータ部の電力が常に変動し、先ほど申しましたようにモータのトルクが変動し、圧縮機の音・振動に影響を及ぼします。影響を抑えるために、何かコンデンサ以外の代替機能によって、電力の変動を吸収しなければならないということです。ダイキン工業は「インバータ波形制御技術」に強みがあります。そこで0.0001秒以下の短い周期でインバータの直流電圧情報とモータ電流情報をフィードバックし、また電源の周波数情報を検出することで、電圧変動で発生する電力脈動を相殺するようにソフトウェアで補償制御を行い、安定化させているのです。これは非常に難しい独自技術なので、他社の追従を許していません。
他社の追従を許さない独自の「インバータ波形制御」により、ソフトウェア的に高調波成分のノイズを除去する代替機能を実現した電解コンデンサレス技術。
――なるほど。ただインバータ自体が高調波成分のノイズを出しやすいということもありますが、影響することはないのでしょうか?
土居:電解コンデンサをレス化すると電源側へ流出する高調波成分の電流に対しても考慮しないといけません。国ごとに高調波電流の規格が異なるため、その国に適合するようにインバータの波形制御で高調波電流を抑制する必要があります。この高調波電流の抑制制御はリアクタの両端に発生する電圧をフィードバックして実現しています。
このようにモータを安定動作させる技術と、高調波成分のノイズを抑える技術を両立させるソフトウェアとハードウェアの技術を持っている点が、ダイキン工業のアドバンテージになっているのです。
「総合格闘技」のインバータ開発だからこそ、関係部署の調整も必要
――電解コンデンサレス技術を確立する際には、どんなハードルがありましたか?
土居:電解コンデンサレス技術は、長寿命化やコストダウンにつながりますが、一方でモータや圧縮機にとっては不利な要素もあり、他部署から異論が噴出しました。たとえば、コンデンサ容量を小さくしたうえで、電力脈動を抑える制御を行うと、その制御にインバータの電圧成分を使うため、その結果、モータ側に使える電圧が低くなり回転数が上がらない、逆に電流を増やすとモータの巻き線の温度が上がってしまうといった懸念事項があり、従来インバータ用のモータ・圧縮機をそのまま使えずに、電解コンデンサレスインバータに合わせたモータ・圧縮機の設計変更が必要になりました。
そのため開発を進める際は、製品全体としてのメリットがある点を示さなければなりませんでした。それを関係部署に伝えることに腐心しました。それが今回一番苦労したところでした。結局、モータの設計を見直し、我々のインバータ仕様に合わせていただきました。そのときは、モータの設計を変更してもメリットが出ることを、具体的な試験データを示しながら丁寧に説明しました。
――実際にどんな説明をして、関係者のみなさんを説得したのでしょうか?
土居:インバータを電解コンデンサレスにすると、モータにかかる電流・電圧、力率などの電気特性が変わってくるため、それに合わせてどんなモータを設計すれば最適になるのか? ということが重要です。とにかく、まずはプロトタイプで電気特性のデータを取り、それが許容範囲なのか確認しながら、少しずつ開発につなげていきました。やはり人間関係の調整が大変でしたね。尖ったことを実現する以上、周囲のコンセンサスを取って進めていかなければなりません。調整には大きなパワーが必要でした。
新しいことに取り組むと、当初の目論見から外れることもあります。プロトタイプなので、チューニングが十分でなく、試験中に停止することもありました。そういうときは現場に測定器を持ち込み、徹底的に原因を究明し、関係部署に辛抱強く説明していきました。インバータ開発は、いわば「総合格闘技」みたいなもので、関係各所の皆さんの協力が絶対に必要です。開発時には厳しいことも言われましたが、最終的には情も伝わりました。困っているときには「こうすれば良いんじゃないの?」とアドバイスもいただきました。
「総合格闘技」のインバータ開発だからこそ、関係部署の調整も必要
――なるほど、まさにやり遂げたという感じでしょうか。技術者冥利に尽きますね。
土居:たくさん苦労しましたが、商品開発に携わった11年間の知識とノウハウを総動員して、良いものに仕上がったと思います。仕事をするうえでは、自分のパフォーマンスを最大限に発揮し、自分では難しいことは他者の力を借りる。どれだけ人を巻き込めるかという点も大切でした。大きな目標に向かい、ビジョンをしっかり見据えて進んでいく大切さも学びました。この電解コンデンサレス技術は、すべてのインバータに応用が可能です。基本特許も取っており、他社も参入できません。
――最後に、これからダイキン工業に入る後輩の皆さんに何かメッセージをいただけますか?
土居:私の業務、特にインバータ系はハードウェア、ソフトウェア制御に関わる技術者がたくさん在籍しており活躍しております。また、モータも圧縮機も要素技術を自前で開発しています。だからこそダイキン工業は、自分の理想を実現できる企業だと思います。インバータの開発も横串を通して各部署と連携し、問題が出たら相談できますし、その対応スピードも早いのです。どんな立場で入社しても、個々のパワーを最大限に引き出してくれる職場が待っています。
Hirotaka Doi
テクノロジー・イノベーションセンター
2005年4月入社。兵庫県出身。インバータのハード技術開発を担当。ダイキン独自のインバータ技術をこれからも世界中に展開していくために、日々挑戦し続けていきたい。
関連記事
関連採用情報